Prescreening Questions to Ask Remanufacturing Process Optimization Specialist
So, you’re knee-deep in finding the perfect candidate for your remanufacturing process optimization role? Great! Let's dive right into a set of comprehensive prescreening questions that aim to uncover the depth of experience, technical know-how, and the soft skills essential for the position. These questions will not only give you a well-rounded view of a candidate’s capabilities but also help you gauge their problem-solving skills and adaptability. Ready? Let’s get started.
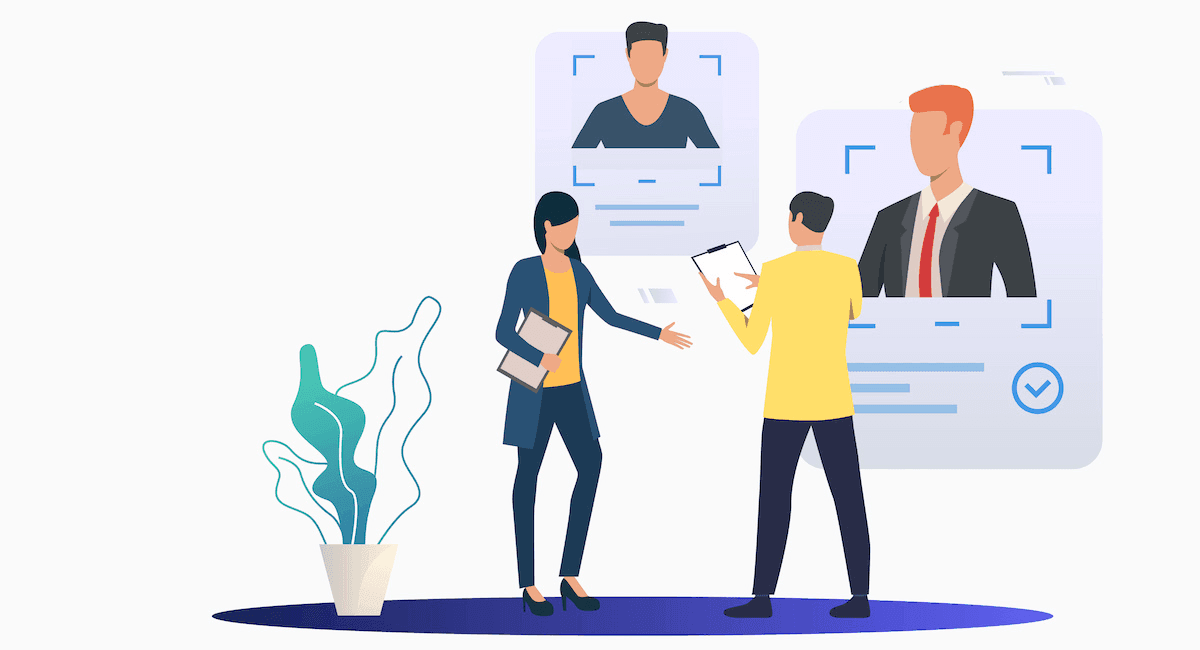
What experience do you have with improving manufacturing processes?
When it comes to manufacturing, experience is key. Ask the candidate to provide specific examples of their prior work, detailing the processes they’ve improved. Were they involved in streamlining assembly lines or perhaps in enhancing the precision of production through robotics? Their response will give you insight into the breadth and depth of their experience.
Can you explain a time when you implemented optimization strategies in a remanufacturing setting?
Stories of past achievements can reveal a lot about a person’s strategic thinking. Have them narrate a particular scenario where they used their optimization skills. Did they manage to save time, reduce costs, or improve product quality? Their story will shed light on their practical capabilities and problem-solving skills in real-world settings.
What methodologies do you commonly use for process optimization?
A candidate proficient in process optimization should be familiar with various methodologies like Six Sigma, Lean Manufacturing, or Kaizen. Ask them to explain how they utilize these methodologies and tailor them to meet specific goals. Their response can help you understand their technical approach and flexibility in adapting methodologies to different situations.
How do you ensure quality control while optimizing remanufacturing processes?
Optimization often involves balancing efficiency with quality. Ask them to explain their strategies for maintaining high standards while pushing for optimization. Are they using statistical process control or automated inspection systems? This will highlight their attention to detail and commitment to quality.
What software tools are you proficient in for process analysis and optimization?
In today’s tech-savvy world, software tools play a significant role in process optimization. Whether it’s ERP systems, simulation software like AutoCAD, or data analysis tools like Minitab, it's crucial to know their level of proficiency. Their familiarity with these tools can be a deal-breaker in modern manufacturing environments.
How would you handle resistance to change from production staff?
Change can be tough, especially in a long-established production environment. Understanding how a candidate plans to manage resistance can reveal their leadership and communication skills. Do they use persuasive communication, training sessions, or involve the staff in decision-making processes? This tells about their ability to foster a collaborative work environment.
Can you describe your experience with lean manufacturing principles?
Lean manufacturing principles are fundamental in reducing waste and improving efficiency. Ask about their experience with concepts like Just-In-Time (JIT), 5S, and Kanban. They should be able to provide examples of how they have implemented these principles to great effect in their past roles.
How do you measure the success of an optimization project?
Metrics and KPIs are critical in determining the success of any project. Look for candidates who talk about tangible outcomes like cost savings, reduced cycle times, higher throughput, or lower defect rates. Their ability to measure success will hint at their results-driven mindset.
What challenges have you faced in remanufacturing process optimization and how did you overcome them?
Challenges are part and parcel of any optimization project. Ask them to narrate specific instances where they hit roadblocks and how they tackled them. Were there technical issues, team resistance, or budget constraints? Their problem-solving skills and resilience will shine through in their response.
How do you stay updated on the latest trends in remanufacturing and process optimization?
The manufacturing world is constantly evolving. Seek out candidates who actively engage in continuous learning through workshops, seminars, industry publications, and online courses. Staying updated reflects their commitment to growth and adaptation in their field.
What is your approach to cost reduction in remanufacturing processes?
Cost reduction without compromising quality is a tricky balance to achieve. Look for answers that detail strategic cost-cutting measures, whether through energy-efficient technologies, bulk material sourcing, or waste reduction techniques. Their approach can reveal their strategic thinking and financial acumen.
How do you balance efficiency and sustainability in remanufacturing?
With increasing emphasis on sustainability, it's important to understand how they plan to marry efficiency with eco-friendly practices. Do they use recyclable materials, reduce energy consumption, or repurpose manufacturing waste? Their answer will speak volumes about their commitment to sustainable practices.
Can you give an example of a project where you significantly reduced waste?
Waste reduction is a key component of process optimization. Ask them to provide a detailed example where their efforts led to substantial waste reduction. This example will highlight their ability to effectively identify and eliminate wasteful practices.
What strategies do you use for minimizing downtime during process changes?
Downtime can be costly. Find out about the strategies they deploy to minimize disruptions during process changes. Do they use phased rollouts, parallel running systems, or preventive maintenance strategies? Their methods will indicate their planning and foresight abilities.
How do you prioritize which processes to optimize first?
Prioritization is crucial in process optimization. Look for answers that demonstrate a logical and strategic approach. Do they start with the most cost-intensive processes, or perhaps those with the highest defect rates? Their prioritization strategy can reveal their analytical and decision-making skills.
What role does data play in your optimization strategies?
Data is the backbone of any optimization effort. Probe into how they collect, analyze, and utilize data in their projects. Are they leveraging big data analytics, utilizing IoT sensors, or running simulations? Their use of data will highlight their technical proficiency and analytical mindset.
How do you handle discrepancies between planned and actual performance after implementing optimizations?
Discrepancies are bound to occur. Ask about their process for managing and correcting deviations from the planned outcomes. Are they running regular audits, engaging in continuous monitoring, or using agile methodologies to iterate rapidly? Their answer will indicate their adaptability and problem-solving approach.
Can you describe a situation where you had to optimize a process under tight deadlines?
Time-critical projects test a candidate's ability to perform under pressure. Ask for specific examples where they faced tight deadlines and managed to deliver. How did they prioritize tasks, manage resources, and what was the outcome? This will reveal their time management and stress-handling capabilities.
What techniques do you use for root cause analysis in process optimization?
Root cause analysis is essential in getting to the heart of process inefficiencies. Seek out candidates who use techniques like Fishbone diagrams, 5 Whys, or Pareto Analysis. Their approach to root cause analysis will show their problem-solving depth and technical understanding.
How do you ensure that optimized processes remain flexible for future changes or upgrades?
In a fast-paced industry, flexibility is paramount. Ask about their strategies for ensuring that optimized processes can adapt to future needs. Do they integrate modular designs, use scalable systems, or engage in continuous improvement cycles? Their focus on flexibility will highlight their foresight and strategic planning skills.
Prescreening questions for Remanufacturing Process Optimization Specialist
- What experience do you have with improving manufacturing processes?
- Can you explain a time when you implemented optimization strategies in a remanufacturing setting?
- What methodologies do you commonly use for process optimization?
- How do you ensure quality control while optimizing remanufacturing processes?
- What software tools are you proficient in for process analysis and optimization?
- How would you handle resistance to change from production staff?
- Can you describe your experience with lean manufacturing principles?
- How do you measure the success of an optimization project?
- What challenges have you faced in remanufacturing process optimization and how did you overcome them?
- How do you stay updated on the latest trends in remanufacturing and process optimization?
- What is your approach to cost reduction in remanufacturing processes?
- How do you balance efficiency and sustainability in remanufacturing?
- Can you give an example of a project where you significantly reduced waste?
- What strategies do you use for minimizing downtime during process changes?
- How do you prioritize which processes to optimize first?
- What role does data play in your optimization strategies?
- How do you handle discrepancies between planned and actual performance after implementing optimizations?
- Can you describe a situation where you had to optimize a process under tight deadlines?
- What techniques do you use for root cause analysis in process optimization?
- How do you ensure that optimized processes remain flexible for future changes or upgrades?
Interview Remanufacturing Process Optimization Specialist on Hirevire
Have a list of Remanufacturing Process Optimization Specialist candidates? Hirevire has got you covered! Schedule interviews with qualified candidates right away.